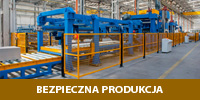
PRONAR zatrudnia ponad 2 tys. osób, których praca jest podstawą sukcesu firmy. Dbałość o zdrowie i bezpieczeństwo zatrudnionych jest fundamentem polityki, która dąży do eliminowania wypadków przy pracy. Jest to realizowane poprzez systemowe zarządzanie bezpieczeństwem i higieną pracy (BHP).
Systemowe zarządzanie BHP w PRONARZE polega na:
• identyfikacji zagrożeń poprzez przeprowadzanie oceny ryzyka i określanie środków kontroli, a także rozwijaniu procesów i procedur mających na celu zmniejszenie i kontrolę ryzyka zagrożeń;
• utrzymywaniu zgodności ze wszystkimi wymogami europejskich i krajowych norm prawnych, szczególnie z Unijną Dyrektywą Maszynową 2006/42/WE;
• przeprowadzaniu odpowiednich szkoleń w celu zapewnienia wiedzy o potencjalnych zagrożeniach i nadaniu pracownikom kompetencji do wykonywania w sposób bezpieczny określonych zadań;
• promowaniu aktywnego udziału wszystkich pracowników i osób zarządzających w wysiłkach na rzecz BHP,
• wykorzystywaniu najnowszych rozwiązań technicznych w zakresie zabezpieczania stanowisk pracy.
Czynniki oddziałujące na pracowników (w miejscu pracy) klasyfikuje się, ze względu na stopień ich uciążliwości, jako: uciążliwe, szkodliwe oraz niebezpieczne. Szkodliwe oraz uciążliwe dzielone są na czynniki: psychofizyczne, fizyczne, zagrożenia chemiczne oraz biologiczne.
Produkcja w PRONARZE polega w dużej mierze na wykorzystaniu przecinarek plazmowych i łączeniu detali za pomocą różnych metod spawania. Jest to proces wysokotemperaturowy, w trakcie którego wokół stanowiska unoszą się iskry i spadają odpryski metali. Zagrożeniem dla operatorów spawarek jest także promieniowanie optyczne, którego źródłem jest łuk elektryczny. Podczas spawania używane są maski automatyczne w celu ochrony oczu i twarzy. Inżynierowie Wydziału Kół Tarczowych skonstruowali zautomatyzowane stanowiska spawalnicze, dzięki czemu pracownik zakłada i odbiera detal z maszyny bez narażania się na zagrożenia. Stosowanie kurtyn spawalniczych chroni przed promieniowaniem ultrafioletowym.
Podczas produkcji może pojawiać się zwiększony poziom hałasu i zapylenia. W związku z tym wszyscy pracownicy są wyposażeni w ochronniki słuchu – wkładki lub nauszniki przeciwhałasowe (ochrona przed hałasem przenoszonym przez powietrze lub przewodnictwo kostne). W obszarach zapylonych istnieje nakaz używania półmasek filtrujących, a na terenie hal produkcyjnych – obowiązek noszenia kasków oraz obuwia ochronnego.
Dla bezpieczeństwa pracowników, którzy mogą mieć kontakt ze szkodliwymi gazami, bardzo ważna jest skuteczna wentylacja hali produkcyjnej. Zapewniają to wysokowydajne wentylatory dachowe oraz okapy wyciągowe (nad stanowiskami spawalniczymi) łącznie z nawiewami świeżego powietrza. Praca w warunkach uciążliwych nie stwarza bezpośredniego zagrożenia doznania urazu albo rozwinięcia się choroby zawodowej, lecz utrudnia wykonywanie obowiązków.
PRONAR podejmuje szereg działań ograniczających występowanie czynników niebezpiecznych – głównie w kontekście automatyzacji i wdrażania rozwiązań bezpieczeństwa. Inżynierowie WKT zaprojektowali i uruchomili wiele nowoczesnych maszyn i linii produkcyjnych, wyposażając je w najnowsze rozwiązania techniczne w dziedzinie bezpieczeństwa.
Przykładem może być nowa, zautomatyzowana linia rozkroju poprzecznego, w której zastosowano kurtyny z funkcją mutingu (tzw. wyciszania) oraz wygrodzenia z kontrolą i blokadą dostępu z wykorzystaniem magnetycznych zamków ryglowanych elektrycznie (blokujących możliwość nieuprawnionego wtargnięcia w obszar niebezpieczny). Oprócz tego zastosowano nowoczesne napędy z zaimplementowanymi funkcjami bezpieczeństwa, zgodnie z zaleceniami odpowiednich norm, np. PN-EN 61800-5-2, dotycząca elektrycznych układów napędowych o regulowanej prędkości, w których można zrealizować m.in. bezpieczne wyłączenie momentu obrotowego – funkcja Safe Torque Off (STO).
Funkcja ta powoduje odłączenie zasilania od silnika, w efekcie czego nie wytwarza on momentu obrotowego albo siły – w wypadku silników liniowych. Jest to podstawowa metoda zapobiegania nagłemu nieoczekiwanemu rozruchowi silnika, powodującemu niekontrolowane przemieszczenie się ruchomych części maszyny. W obwodach zatrzymania awaryjnego zastosowano podświetlane wyłączniki bezpieczeństwa, spełniające wymogi normy PN-EN ISO 13850 o jasnej informacji o stanie e-stopu. Stosowane systemy bezpieczeństwa bazują na rozwiązaniach renomowanych firm.
Kolejnym przykładem automatyzacji w kontekście bezpiecznej produkcji są zrobotyzowane gniazda spawalnicze ze zautomatyzowanym pobieraniem i wydawaniem gotowych obręczy i kół. Zostały one wyposażone w nadzorowane wygrodzenia, bariery optyczne z funkcją mutingu, maty bezpieczeństwa, pozwalające na wejście lub wyjście detalu przez światło kurtyny bez zatrzymywania pracy aplikacji. Gdyby jednak pracownik próbował się przedostać do obszaru niebezpiecznego, wiązki kurtyn od razu go wykryją i zatrzymają pracę aplikacji. Wszystkie te systemy mają na celu zapobieżenie nieuprawnionemu dostępowi do stref niebezpiecznych, jednocześnie nie zakłócając procesu technologicznego. Tego typu zabezpieczenia zastosowano też w automatycznej zwijarce pasów blach w obszarze załadunku oraz odbioru detali.
Nadrzędnym celem PRONARU jest eliminacja zagrożeń i tworzenie bezpiecznych stanowisk pracy na rzecz poprawy jakości i wydajności procesu produkcji. Automatyzacja pozwala na wyręczenie pracownika w ciężkich i niebezpiecznych czynnościach, dzięki czemu chronione jest jego zdrowie, a firma odnosi korzyści ze zwiększającej się wydajności pracy i zmniejszającej się absencji pracowników, co jest odzwierciedleniem polityki PRONARU oraz kierunkiem rozwoju firmy.
Tomasz Kropiewnicki
Autor jest konstruktorem-automatykiem na Wydziale Kół Tarczowych w PRONARZE